Толщина стены из бетона. От чего она зависит? Пустотные стены из железобетона: устройство и применение, подпорная монолитная стена, опалубка и армирование стен, фото и видео
Процесс возведения фундаментов и стен из монолитного железобетона включает разбивку осей фундаментов, устройство опалубки, сборку и установку арматуры и бетонирование фундамента.
Выбор технологии возведения фундаментов из монолитного железобетона зависит от конструктивных решений фундаментов и зданий, а также от имеющегося технологического оборудования и механизмов.
Разбивка осей фундаментов из монолитного железобетона производится так же, как и при возведении сборных фундаментов.
Трудоемкость и стоимость устройства монолитных фундаментов, выполняемых в опалубке, в значительной степени зависят от модуля поверхности фундамента М. С увеличением модуля поверхности возрастает трудоемкость всех процессов, особенно опалубочных работ.
Выбор типа опалубки зависит от вида бетонируемых конструкций и их повторяемости и производится на основе технико-экономических расчетов по возможным вариантам. Определяющими показателями являются- затраты материалов и труда, а также себестоимость одного оборота опалубки.
Исследование расхода материалов, трудоемкости Т0 и себестоимости различных типов опалубок в зависимости от оборачиваемости п0 наглядно показывает эффективность инвентарных комбинированных и металлических опалубок с большой оборачиваемостью.
Инвентарная опалубка бывает деревянной, металлической и комбинированной. Применение инвентарной опалубки позволяет сократить затраты труда на опалубочных работах в 1,5-2 раза и снизить расход материалов.
Опалубка может быть выполнена из отдельных щитов, укрупненных пространственных блоков, панелей и армоопалубочных блоков.
Опалубку из отдельных щитов применяют при сложной геометрической форме фундамента и при небольшой повторяемости типов фундаментов. Разборно-переставная щитовая деревянная опалубка может выполняться из мелких и крупных щитов
Опалубку из мелких щитов на сшивных планках применяют при устройстве мелких и средних по объему ленточных и столбчатых фундаментов.
Щиты опалубки крепят к ребрам гвоздями и болтами или планками и штырями. Для воспринятая бокового давления бетонной смеси щиты крепят проволочными скрутками или болтами. На собранной в блок опалубке намечают середину короба, поверх которого прибивают накрест рейки, таким образом, чтобы грани реек располагались по осям. Собранный блок подают краном к месту установки и рейки совмещают с натянутыми осями. После выверки опалубку закрепляют, а рейки удаляют.
При устройстве опалубки высоких ступенчатых фундаментов установку вышележащих блоков опалубки производит аналогично.
Опалубка из мелких щитов устанавливается отдельными щитами вручную. Оборачиваемость ее не более 5-7-кратной.
При больших размерах фундаментов и стен разборно-переставная щитовая деревянная опалубка собирается из крупных щитов на месте устройства фундамента. Опалубка крепится подкосами, схватками и болтовыми стяжками.
Щиты комбинированной опалубки УКО-67 конструкции ЦНИИОМТП состоят из стального каркаса, сваренного из уголков, и палубы из досок. Крепление щитов производится быстроразъемными соединениями. При проектировании щитов комбинированной опалубки принят модуль 600 мм.
Инвентарную комбинированную опалубку серии УКО-67 применяют при бетонировании мелких и средних фундаментов. В комплект опалубки входят: основные щиты восьми типоразмеров, угловые щиты двух типоразмеров, схватки четырех типоразмеров, а также монтажные уголки, несущие фермы, инвентарные приспособления для сборки щитов. Оборачиваемость 100-кратная.
При возведении монолитных фундаментов применяют также опалубки серии УСО-67, «Монолит-72» и другие типы.
При большой повторяемости фундаментов небольшого объема и простой формы применяют инвентарные металлические блок-формы, которые устанавливают на место краном.
Блок-формы изготовляются неразъемными, распалубка которых производится целиком в раннем возрасте конструкции (до 24 ч), и разъемными, демонтируемыми по элементам.
Трестом «Уралалюминстрой» для бетонирования фундаментов использовалась инвентарная стальная опалубка, которая собиралась из пространственных блоков или крупных щитов. Опалубка ФМ-2 имела четыре уступа, причем каждый собирался из четырех щитов, ребра жесткости которых сделаны из угловой стали сечением 50X Х50Х6, а палуба из листовой стали толщиной 8 мм. В полках уголков просверлены отверстия для крепления щитов между собой. Пространственный блок собирали в мастерской и в готовом виде транспортировали к месту установки. После окончания бетонирования блок не разбирают, а в собранном виде поднимают краном, предварительно оторвав его от бетона при помощи четырех домкратов, установленных в нижних углах блока.
Конструкция опалубки ФМ-12 предназначена для фундаментов большой высоты. Она состоит из двух уступов и короба для подколонника с выступами для ранд-балок. Нижние два уступа выполнены аналогично опалубке ФМ-2. Верхний короб состоит из четырех щитов, .которые крепятся между собой болтами. Опалубку на объекте собирают с помощью крана. Большая высота подколонника и наличие двух выступов не позволяют снимать опалубку без ее разборки, поэтому ее разбирают на отдельные щиты.
На строительстве одного из цехов металлургического завода при возведении отдельно стоящих фундаментов применяли опалубку, собираемую из 2-3 пространственных блоков. Такую опалубку, имеющую общую высоту до 2,5 м снимали с фундамента в собранном виде. Опалубки высотой 3-5 м снимались частями. Сначала снимались крепления между нижними и верхними блоками. Полной разборки верхнего блока не делалось. Перед его подъемом краном болтовые соединения между щитами, образующими блок, ослаблялись. Нижний блок снимался целиком без разборки.
Блоки опалубки изготовляли из стальных щитов, которые крепились с помощью болтов. Ребра жесткости щитов выполнялись из угловой стали, сечение которой подбиралось в зависимости от нагрузки. Для увеличения жесткости щитов снаружи к листу приваривают ребра жесткости из полосовой стали.
Находят также применение трансформирующиеся блок-формы, которые изменяют свои размеры и форму путем раздвижки формы с последующей фиксацией элементов специальными устройствами.
В практике строительства в некоторых случаях находит применение несъемная опалубка из плоских и пространственных железобетонных элементов. Такая опалубка может применяться при возведении столбчатых фундаментов, когда по условиям производства затруднительно демонтировать опалубку или необходимо в сжатые сроки произвести обратную засыпку котлованов. Ступенчатая часть фундаментов может выполняться в обычной или несъемной опалубке.
При возведении столбчатых фундаментов высотой до 5 м применяются плоские плиты толщиной 60-90 мм. Опалубку нижней части ступенчатого фундамента собирают из плоских плит, которые устанавливают на бетонную подготовку путем сварки закладных деталей в углах. Затем укладывают арматурную сетку и монтируют армокаркас подколонника, после чего монтируют плиты последующих ступеней и подколонника.
При устройстве опалубки необходимо обеспечивать ее устойчивость и неизменяемость геометрической формы в процессе бетонирования фундамента. Для этого стойки и другие
несущие элементы опалубки устанавливают на надежное основание, а стойки также закрепляют горизонтальными и диагональными расшивками. Правильность устройства опалубки должна быть проверена до начала установки арматуры.
Снижение трудоемкости опалубочных работ может быть обеспечено за счет унификации и сокращения числа типоразмеров фундаментов; за счет применения инвентарной многообора-чиваемой опалубки, благодаря широкому использованию механизированного монтажа опалубки из укрепленных элементов. При большой повторяемости однотипных фундаментов опалубка собирается один раз и после бетонирования одного фундамента переносится на следующий. При использовании блок-форм уровень механизации опалубочных работ составляет 90-95 %.
Отдельно стоящие фундаменты армируют арматурой классов A-I, А-II, A-III, B-I диаметром 8-22 мм.
Монтаж арматуры выполняют укрупненными элементами в виде сеток и пространственных каркасов, которые подают к месту установки самоходными кранами с помощью специальных траверс. Для монтажа каркасов фундаментов и подколонников большой массы при высоте более 2 м применяют самобалансирующиеся стропы.
Нижнюю арматурную сетку фундамента устанавливают до монтажа опалубки. Арматурный каркас подколонника может быть смонтирован как до установки опалубки, так и после.
Отдельные стержни сеток и каркасов на месте их установки должны быть состыкованы электрошлаковой или ванной сваркой.
Затраты труда на возведение 1 м3 фундаментов из монолитного железобетона составляет 3-5 чел.-ч. Наиболее трудоемкими являются опалубочные и арматурные работы. Снижение трудоемкости возведения фундаментов может быть достигнуто за счет применения арматурно-опалубочных блоков с приваренными к ним закладными деталями.
При возведении ленточных фундаментов применяют различные схемы комплексной механизации.
Армирование начинают с укладки арматурных сеток у подошвы фундамента. Для создания защитного слоя бетона устанавливают фиксаторы в шахматном порядке с шагом 1 м. Затем устанавливают арматурные каркасы и закрепляют с помощью фиксаторов. Временные крепления с каркасов снимают после их приварки к сетке подошвы фундамента. Затем производят монтаж опалубки.
Опалубку ленточных фундаментов постоянного поперечного сечения собирают в зависимости от высоты фундамента. При высоте 2-2,5 м щиты устанавливают последовательно вертикально, соединяя их между собою на замках, и временно раскрепляют инвентарными подкосами. К ним присоединяют схватки, а затем опалубочные плоскости соединяют стяжками. Щиты второго яруса закрепляют на нижних после рихтовки опалубках и располагают их горизонтально.
При высоте фундамента более 2,5 м сборку опалубки начинают с установки каркаса из схваток. Монтажная устойчивость вертикально располагаемых схваток обеспечивается в начале сборки с помощью подкосов из телескопических стоек, а затем за счет горизонтальных связей, выполняемых из тех же схваток. Подкосы устанавливают через 3-4 м. Выше уровня бетонируемого фундамента схватки соединяют стяжками и раскрепляют распорками, что обеспечивает всему каркасу пространственную устойчивость. Щиты присоединяют к схваткам и располагают горизонтально. Они могут быть установлены на всю высоту фундамента с обеих сторон или с одной стороны на часть высоты, облегчая производство арматурных и бетонных работ.
Мелкощитовая или крупнощитовая опалубка ленточных фундаментов переменного поперечного сечения устанавливается также по двум схемам. При небольших размерах фундаментов сначала собирается опалубка нижней части фундамента. Верхняя часть опалубки может быть установлена после бетонирования нижней части фундамента.
По второй схеме предусматривается подвеска верхней части опалубки за схватки к порталам. Арматурные сетки укладывают до установки стяжек, которые соединяют опалубочные плоскости.
Перед укладкой бетонной смеси необходимо тщательно подготовить грунтовое основание. Рыхлые, органические и илистые грунты должны быть удалены. Переборы грунта следует заполнить уплотненным песком или щебнем. Подлежат удалению также продукты выветривания скальных оснований.
Для возведения фундаментов используют тяжелый бетон классов В15-ВЗО. Подвижность бетонной смеси должна соответствовать осадке конуса для неармированных и малоармированных фундаментов 10-30 мм, при перемещении ленточными конвейерами-не выше 60 мм, при транспортировке бетононасосами 50-80 мм.
Наибольший размер зерен крупного заполнителя в бетонной смеси не должен превышать 1/3 наименьшего размера конструкции, а в армированных конструкциях-3/4 наименьшего расстояния в свету между стержнями арматуры.
Для достижения монолитности железобетонных фундаментов бетонирование необходимо вести непрерывно, не допуская образования швов.
Бетонную смесь укладывают горизонтальными слоями толщиной 20- 50 см, причем толщина слоя не должна превышать 1,25 длины рабочей части вибратора. Каждый последующий слой бетонной смеси укладывают после уплотнения предыдущего и, как правило, до начала его схватывания. Для получения однородной степени уплотнения необходимо соблюдать расстояния между каждой постановкой вибратора, которое не должно превышать 1,5 радиуса действия вибратора. При уплотнении слоя глубинный вибратор должен проникать на 10-15 см в ранее уложенный слой, в результате чего достигается более надежное сопряжение бетонируемых слоев.
Бетонную смесь в малоармированных фундаментах уплотняют глубинными вибраторами С-825 и С-826, а также вибропакетами. При густом армировании применяют вибраторы С-727, С-800 или другие с гибким валом.
При бетонировании столбчатых фундаментов со стороны сечения подколонника 0,4-0,8 м и при отсутствии пересекающихся хомутов высота свободного падения бетонной смеси допускается до 5 м, при размерах сторон 0,8-3 м. При большей высоте фундамента применяют хоботы.
Фундаменты с подколонниками,армированными перекрещивающимися хомутами, бетонируют непрерывно участками высотой 1,5-2 м с подачей смеси через окна, устраиваемые в боковых стенах опалубки.
Бетонирование столбчатых фундаментов под колонны осуществляется в два или три этапа.
В два этапа бетонируются небольшие (10-15 м3) фундаменты. Первоначально заполняют опалубку ступенчатой части. Уплотняют бетонную смесь вибратором. Затем продолжают укладку бетонной смеси в подко-лонник до низа стакана под колонну или низа анкерных болтов, а на втором этапе бетонируется верх подколонника после установки пустотооб-разователя стакана или анкерных болтов. При трехэтапном бетонировании крупных фундаментов укладка бетонной смеси в нижние ступени и подко-лонник осуществляется раздельно.
При бетонировании фундамента сразу на всю высоту в зоне перехода ступенчатой части в подколонник возможно образование усадочных трещин, что может снизить несущую способность фундамента. Чтобы предотвратить образование усадочных трещин по окончании бетонирования ступеней делают технологический перерыв для набора прочности бетоном и его усадки. Затем бетонируют подколонник.
Стакан фундаментов бетонируют ниже проектной отметки, чтобы в последующем при установке колонны можно было выполнить подливку под проектную отметку колонны.
Анкерные болты устанавливают перед бетонированием с использованием кондукторов, закрепленных на опалубке или каркасе, остающемся в массиве бетона. Конструкция кондуктора должна исключать возможность отклонения болтов от проектного положения во время бетонирования.
При устройстве фундаментов применяют также метод безопалубочного бетонирования, который заключается в том, что в построечных условиях изготовляют арматурно-опалубочные блоки с несъемной опалубкой. Готовый блок устанавливают краном в проектное положение и затем заполняют бетонной смесью. Этот метод может быть использован при устройстве подколонников и стен подземных сооружений. Арматурный блок с закрепленными на нем закладными деталями и фиксаторами защитного слоя доставляют к специальному стенду, расположенному у места установки. Стенд представляет собой площадку, выложенную железобетонными плитами, на которой устанавливают металлическую ванну высотой и размерами в плане, несколько больше боковой грани блока. Арматурный блок устанавливают краном в ванне и с помощью вибраторов втап-ливают в бетон до тех пор, пока фиксаторы защитного слоя не коснутся поверхности стенда. После того как бетон наберет необходимую прочность, блок извлекают из ванны и погружают в слой бетона следующей гранью. Готовый блок устанавливают в проектное положение, выполняют обратную засыпку и бетонируют.
Ленточные фундаменты бетонируют в зависимости от конструктивных особенностей в один, два и три этапа.
Одноэтапное послойное бетонирование применяется при устройстве ленточных фундаментов прямоугольного сечения враспор или переменного сечения при площади поперечного сечения менее 3 м2. Ленточные фундаменты со ступенями при площади поперечного сечения более 3 м2 бетонируют в два этапа, сначала ступени, а затем стену. В три этапа бетонируют ленточные фундаменты с подколенниками, применяемыми в каркасных зданиях.
Особенности бетонирования стен подземной части здания зависят от толщины и высоты стен, а также вида опалубки.
При бетонировании стен применяются следующие виды опалубки: унифицированная щитовая панельная разборно-переставная, подъемно-переставная и другие виды опалубок.
Разборно-переставная щитовая опалубка устанавливается в два приема: вначале с одной стороны на всю высоту стены, а после установки арматуры-с другой. При большой высоте и толщине стены опалубку второй стороны устанавливают поярусно в процессе бетонирования. Если опалубку устанавливают на всю высоту стены, то в опалубке предусматривают отверстие для подачи бетонной смеси. Опалубку стен толщиной более 0,5 м можно возводить на всю высоту стены с подачей смеси сверху с помощью хоботов.
Для обеспечения устойчивости опалубку стен крепят подкосами или расчалками, стяжными болтами и проволочными стяжками. Распорки, установленные внутри опалубки удаляются в процессе бетонирования стен. При поярусном бетонировании стен панели второго и третьего ярусов могут опираться на нижестоящие или на опоры после демонтажа панелей первого яруса. Опоры для панелей второго и третьего ярусов собирают из телескопических или решетчатых стоек.
Технология бетонирования стен зависит от конструкции опалубки. Может быть предусмотрена поярусная укладка бетонной смеси на высоту 400-600 мм. Работы цикла бетонирования выполняют в такой последовательности: вначале устанавливают леса, затем обрабатывают рабочий шов бетонирования, устанавливают арматуру, после чего переставляют опалубку с нижнего яруса на верхний. Цикл заканчивают укладкой и уплотнением бетонной смеси и выдерживанием бетона в опалубке.
При бетонировании стен в разборно-переставной опалубке высота участков, выполняемых без перерыва, не должна превышать 3 м. При большей высоте участков стен, бетонируемых без рабочих швов, необходимо устанавливать перерывы продолжительностью не менее 40 мин, но не более 2 ч для осадки бетонируемой смеси и предупреждения образования осадочных трещин. При длине стены более 20 м ее делят на участки по 7-10 м и на границе участков устанавливают деревянную распределительную перегородку. Бетонную смесь подают в опалубку в нескольких точках по длине участка. Если в стене предусмотрен проем, то бетонирование следует прерывать на уровне верхнего края проема или выполнить в этом месте рабочий шов. Образовавшиеся рабочие швы необходимо тщательно обрабатывать перед бетонированием.
Подачу бетонной смеси осуществляют бадьями, виброжелобами, бетононасосами. При высоте стен более 3 м используют звеньевые хоботы. Бетонную смесь укладывают непрерывно толщиной 0,3-0,5 м с обязательным уплотнением вибраторами. В процессе бетонирования следят за положением арматуры и предотвращают ее смещение, от проектного положения. Следующий по высоте участок бетонируют после набора прочности бетона не менее 0,15 МПа. В тонкие и густоармированные стены укладывают более подвижные бетонные смеси (6-10 см).
Бетонная смесь в опалубку фундаментов может подаваться кранами, бетоноукладчиками и бетононасосами. Наибольшее распространение получила укладка бетонной смеси в бадьях с помощью кранов.
Доставка бетонной смеси к месту укладки осуществляется автобетоновозами и автобетоносмесителями. Для приема бетонной смеси в зоне действия крана укладывают два дощатых настила размером 2,4X3,3 м. На настил вплотную одну к другой устанавливают поворотные бадьи. Для бетонирования отдельно стоящих фундаментов небольшого объема и стен рекомендуется применять бадьи вместимостью 0,5-1 м3. Для фундаментов средних объемов рекомендуется применять бадьи вместимостью 1-2 м3. Применение поворотных бадей исключает необходимость сооружения и разборки эстакад и улучшает использование кранового оборудования. Производительность кранов при подаче бетонной смеси в бадьях составляет 25-100 м3 в смену.
Башенные краны целесообразно использовать при бетонировании фундаментов значительного объема и темпах бетонирования более 50 м3 в смену. Самоходные стреловые полноповоротные краны целесообразно применять для бетонирования отдельно стоящих фундаментов при темпах бетонирования 25- 100 м3 в смену. Расстояние между траншеями и котлованами дает возможность устраивать временные дороги для передвижения самоходных стреловых кранов.
Пример устройства фундаментов под колонны промышленного здания с использованием самоходного стрелового крана. Работа по устройству фундаментов была организована следующим образом. Так как расстояние между осями фундаментов было 6 м, то земляные работы выполнялись в виде общей траншеи. После устройства щебеночной подготовки краном К-161 укладывали арматурные сетки, а затем опалубочные блок-формы из одного или нескольких блоков. По периметру верха фундаментов устанавливали инвентарные мостики и площадки. Один конец мостика опирался на бровку котлована, а другой - на верхний блок опалубки. К верхней части опалубки крепили кронштейны, на которые укладывали щиты настила, образующие подмости.
Рабочая площадка и мостик ограждались. После устройства площадок устанавливались арматурные каркасы подколонников.
Бетонирование осуществляли с использованием крана К-161. Бетонную смесь выгружали из автомобилей-самосвалов в три вибробадьи вместимостью по 0,8 м3. Уплотнение бетонной смеси производили глубинными вибраторами.
В верхней части подколонника устанавливали анкерные болты для крепления стальных колонн с помощью инвентарных кондукторов.
Инвентарный кондуктор сваривался из труб диаметром 60 мм и имел подвижные зажимы для закрепления болтов и выдвижные стойки, присоединяемые к опалубочному блоку. Анкерные болты крепили на подвижных зажимах при помощи гаек. В горизонтальной плоскости болты выверяли подвижными зажимами, а в вертикальной-при помощи выдвижных стоек, по которым опускали или поднимали кондуктор.
Опалубку демонтировали через 4- 5 ч после окончания бетонирования фундамента. Это достигалось путем применения жестких бетонных смесей (осадка конуса 2-4 см). При демонтаже опалубочные блок-формы предварительно отрывали домкратами.
Бетонирование фундаментов проводилось в две смены, в каждой смене работало звено из четырех человек: крановщика, двух монтажников-бетонщиков 3-4-го разряда и стропальщика.
Монтажники-бетонщики в первую смену готовили основание под установку опалубки, демонтировали ее с забетонированного фундамента и монтировали опалубку. Стропальщик зацеплял детали, очищал и смазывал формы, а также участвовал в сборке опалубки и подготовке основания. Второе звено, имеющее такой же состав рабочих, во вторую смену укладывало бетонную смесь. Стропальщик осуществлял приемку бетонной смеси и зацеплял бадьи со смесью. Двое монтажников-бетонщиков укладывали и уплотняли бетонную смесь при помощи вибраторов. Они же устанавливали анкерные болты.
При полной организации возведения фундаментов выработка на одного рабочего по укладке бетонной смеси составила 5-7 м3/смену.
При более высоких темпах бетонирования (50-150 м3 в смену) целесообразно использовать бетоноукладчики и вибротранспортное оборудование
Самоходный бетоноукладчик представляет собой ленточный конвейер, смонтированный на тракторе или экскаваторе и движущийся по верху котлована. Для приема бетонной смеси бетоноукладчик снабжен приемным вибробункером, который выдает бетонную смесь на ленту конвейера через дозирующий затвор. При бетонировании фундаментов и стен, расположенных ниже поверхности земли, для транспортирования бетонной смеси могут быть использованы виброжелоба. Кроме виброжелобов используется вибробункер, промежуточные воронки, подставки и подвески для виброжелобов.
При применении авто бетононасосов бетонная смесь из автобетоносмесителя через разгрузочную воронку подается в приемный бункер бетононасоса, из которого по бетонопрово-ду стрелы направляется к месту укладки. Концевое звено бетонопровода снабжено гибким рукавом, обеспечивающим подачу бетонной смеси в каждый фундамент. Транспортирование бетонной смеси по трубопроводам должно быть непрерывным, чтобы она не схватывалась и не загустевала.
Основными достоинствами подачи бетонной смеси по трубам из-за их гибкости и маневренности являются высокая производительность и возможность подачи смеси на большие расстояния (до 400 м).
Производство бетонных работ должно быть организовано так, чтобы с одной стоянки можно было выполнить наибольший объем работ, использовав при этом магистральный бетонопровод без его разборки. Бе-тонопровод должен монтироваться так, чтобы обеспечить подачу бетонной смеси с наиболее удаленных фундаментов с постоянным приближением к фундаментам, расположенным у бетононасосной установки. При подаче бетонной смеси на большую высоту автобетононасос подключают к магистральному бетонопроводу.
Крупнощитовую опалубку фундаментов и стен снимают кранами с помощью рычажных приспособлений. Оборачиваемость опалубки зависит от качества распалубки. Если блочная опалубка выполнена неразъемной для бетонирования небольших по объему фундаментов (4-6 м3), то демонтаж ее производят после достижения бетоном прочности 1 -1,5 МПа.
По окончании бетонирования фундаментов и стен выполняют исполнительную съемку в точках пересечения осей и через 5-10 м в промежутках между осями. На исполнительную схему наносят отметки и фактические отклонения осей фундаментов и стен от проектного положения в плане.
При устройстве фундаментов в зимнее время могут быть использованы следующие способы выдерживания бетона: способ термоса, способ термоса с применением ускорителей твердения бетона, применение проти-воморозных добавок, предварительный электроразогрев, электропрогрев, применение греющей опалубки и другие способы.
Метод термоса заключается в использовании тепла, выделяющегося в процессе гидратации цементных зерен, а также тепла, внесенного в бетон в момент его приготовления (нагрев воды и заполнителей).
С целью ускорения твердения бетона в ее состав вводят добавки-ускорители твердения: сульфат натрия, хлорид кальция, нитрат кальция.
Паропрогрев производят с использованием паровых рубашек, капиллярной опалубки, паровых бань или труб.
Предварительный электроразогрев бетонной смеси - это дополнительный ее нагрев до максимально возможной температуры перед укладкой в опалубку. Применение предварительного электроразогрева позволяет увеличить период остывания забетонированной конструкции, а следовательно, обеспечить более высокую прочность бетона к моменту его замерзания по сравнению со способом термоса.
Сущность электродного прогрева состоит в том, что электрический переменный ток, проходя между электродами через бетонную смесь, обладающую электрическим сопротивлением, выделяет тепло, которое нагревает бетон в период набора им прочности.
Инфракрасный обогрвв основан на использовании тепловой энергии инфракрасного излучения, которое подают на открытые или опалубленные поверхности фундаментов или стен.
Возведение монолитных фундаментов и стен должно выполняться комплексно-механизированным способом, при котором все трудовые процессы выполняют с помощью специально подобранных комплектов машин. При этом должна обеспечиваться непрерывность производства и требуемый темп работ.
При устройстве фундаментов можно выделить три потока: армирование, установка опалубки и бетонирование.
Ведущим процессом при устройстве фундаментов является бетонирование, поэтому количество рабочих в каждом потоке определяется по ведущему потоку таким образом, чтобы работа во всех потоках шла в одном ритме.
Для организации поточной работы фундаменты и стены разбивают на захватки, в качестве которых может служить пролет, часть пролета или фундаменты по одной оси. Каждое звено, выполнив работы на одной захватке, переходит на другую, а его место занимает звено следующего потока.
Процесс бетонирования фундаментов включает в себя процессы транспортирования, подачи, приема, распределения и уплотнения бетонной смеси. Комплект машин для бетонирования подбирают исходя из требуемого типа укладки бетона с учетом условий доставки бетонной смеси и конструктивных особенностей возводимых фундаментов и стен подземной части здания.
В соответствии с производительностью ведущего потока подбирают комплекты машин для частных потоков по монтажу опалубки, арматуры, приготовлению бетонной смеси.
Целесообразно подбирать систему машин так, чтобы с помощью ведущей машины, например крана, выполнять наибольшее число операций в ведущем и в частных потоках. При расчете потока следует учитывать сроки распалубки фундаментов, так как они определяют общую продолжительность работ и необходимое число комплектов опалубки. Для сокращения сроков распалубки применяют методы ускоренного твердения бетона, например, предварительный электроразогрев бетонной смеси, введение добавок, термоактивную опалубку и др.
В технологических нормах ППР по возведению монолитных фундаментов дают развертки инвентарных щитов опалубки, места установки соединительных замков и креплений, а также доборных элементов. Приводят графики движения комплектов опалубки по мере бетонирования и выдерживания бетона в фундаментах. На схемах указывают места установки подъемных механизмов, бетоноукладчиков, бетононасосов, складирование материалов, схемы движения механизмов и автотранспорта, доставляющего бетонную смесь.
Для определения потребности в материально-технических ресурсах можно воспользоваться данными, приведенными в табл. 6,1, в которой предусмотрено несколько типов ведущих машин и вариантов бетонирования.
Традиционные конструкции фундаментов из монолитного железобетона обладают повышенной материалоемкостью, так как выполняются массивными. Прочностные свойства железобетона используются не полностью, что является одним из основных недостатков. Уменьшения объема фундаментов можно достичь устройством в теле фундамента пустот, а также применением тонкостенных конструкций. В монолитных фундаментах колонн экономия бетона при образова- нии пустот возрастает с увеличением глубины заложения фундамента: при глубине 1,5-2 м экономится 3-7 % бетона; при глубине 2-4 м - 5- 15 % и при глубине свыше 4 м- 20 % и более.
Анализ проектных решений фундаментов промышленных зданий показывает значительное число типоразмеров по каждому объекту. Иногда на каждый типоразмер приходится по 3-5 фундаментов. Многообразие типов фундаментов затрудняет типизацию технологии их возведения и не способствует повышению производительности труда.
Предисловие
Упрощенно технология возведение монолитных стен заключается в следующем: в специальную форму-опалубку, которая имеет контуры будущего строения, устанавливают железную арматуру и заливают бетонную смесь. Когда она застывает, элементы опалубки разбирают и переносят на следующий уровень (этаж).
Необходимые инструменты и материалы
Арматура
Бетономешалка
Болгарка
Ведро
Вода
Гвозди
Гвоздодер
Доска строганная
Керамзит
Лопата
Мастерок
Песок
Рубероид
Рулетка
Саморезы
Угольник
Удлинитель
Уровень
Цемент
Cодержание
Монолитный дом – самое прочное строение, способное выдержать даже небольшие колебания почвы. Ещё пару десятилетий назад было принято применять технологию устройства монолитных стен только для серьезных промышленных объектов и многоэтажных жилых домов. Но теперь все чаще возведение монолитных стен практикуется и в частном загородном строительстве.
Упрощенно технология возведение монолитных стен заключается в следующем: в специальную форму-опалубку, которая имеет контуры будущего строения, устанавливают железную арматуру и заливают бетонную смесь. Когда она застывает, элементы опалубки разбирают и переносят на следующий уровень (этаж). Роль опалубки может выполнять и кирпич, это позволяет получить стену, поверхность которой не нуждается в дальнейшей отделке или облицовке. Кроме того, при устройстве монолитных стен опалубка может быть комбинированной: для наружной поверхности стены кирпичная, а внутри-съемная, из металлических или деревянных щитов. Правда, это несколько снижает несущую способность стены, но для возведения одно-, двух- или даже трехэтажных загородных домов это самый оптимальный вариант.
Стены малоэтажных жилых зданий не испытывают большой нагрузки. Поэтому в качестве бетонной смеси по технологии строительства монолитных стен обычно используют легкие бетоны. Такие смеси делают из наполнителя: шлака, керамзита, пенопласта, кирпичного боя, древесных опилок и соломы с применением в качестве вяжущего вещества цемента, а иногда даже извести, глины и гипса. Но обычно их используют в качестве добавок, что сокращает расход цемента и делает смесь более пластичной и удобной для кладки. Благодаря наполнителям легкий бетон по своим теплозащитным качествам гораздо лучше полнотелого кирпича, а по стоимости намного дешевле его. Стены из легкого бетона относительно долговечны, но имеют не очень презентабельный внешний вид и нуждаются в хорошей влагозащите (то есть требуют дальнейшей ).
Толщина стен монолитного дома и выполнение опалубки
Толщина стен монолитного дома во многом зависит от расчетной температуры наружного воздуха. Для стены толщиной 250 мм она равна -20°С, 350 мм -30 °С и 450 мм -40 °С.
Для удобства при выполнении работ элементы опалубки делают высотой 40-60 см. Это могут быть листы ДСП, металлические и деревянные щиты. При необходимости, изнутри щиты покрывают синтетической пленкой или пергамином. В процессе работы щиты прижимают к стойкам, установленным с обеих сторон возводимой стены на всю ее высоту. Расстояние между соседними стойками не должно превышать 1,5 м. Каждая пара стоек, расположенных одна против другой, поверху стягивается проволочными скрутками, а внутрь опалубки устанавливаются временные распорки.
В наши дни в загородном домостроении технология строительства монолитных стен из бетона предусматривает использование несъемной опалубки. Возведение монолитной стены фактически представляет собой комбинацию монолитного домостроения и кладки из пустотных блоков. В данном случае блоки выполняют функции опалубки, однако, в отличие от сборно-разборной конструкции, они не демонтируются по достижении бетонной смесью необходимой прочности, а становятся частью стены. В результате, такая технология позволяет значительно ускорить темпы возведения стен, без снижения их качества. Более того, блоки, играющие роль опалубки, могут быть изготовлены из теплоизолирующего материала, например пенополисгирола (пенопласта), что позволяет одновременно с возведением стены решить задачу по ее утеплению.
Обычно блоки для несъемных опалубок представляют собой две пластины, соединенные между собой специальными стяжками. Основным элементом блочной системы является базовый стеновой модуль нескольких типоразмеров.
Кроме того, система обычно включает угловые блоки, торцевые заглушки, а также дополнительные элементы, например блок с выступом для кирпичной кладки, конический блок и др.
Возведение монолитных стен дома
Возведение монолитных стен дома начинают с установки угловых блоков, между ними натягивают шнур, по которому выкладывают блоки ряда. При этом их не скрепляют между собой раствором (как обычно делают при кладке стен из традиционных бетонных блоков или кирпича) - от смещения их удерживают имеющиеся на торцевых плоскостях пазы и гребни.
В качестве армирующих элементов используются вертикальные и горизонтальные стержни из арматуры диаметром 8-10 мм. Затем кладут второй ряд блоков, надевая их на торчащую из нижнего ряда вертикальную арматуру, и вновь укладывают продольную арматуру и связывают ее с вертикальными стержнями тонкой проволокой. Перевязку делают смещением верхнего ряда на половину блока. После того как собраны 3-4 ряда, внутреннее пространство блоков заполняется одной из описанных выше смесью легкого бетона, которая после затвердевания образует монолитную стену. Как утверждают специалисты, стены таким методом можно возвести чрезвычайно быстро и для этого не требуется высокой квалификации.
Здания с несущими стенами из монолитного железобетона следует проектировать с продольными и поперечными стенами, объединенными перекрытиями в единую пространственную систему.
Здания с несущими стенами из монолитного железобетона рекомендуется проектировать с применением перекрестно-стеновых конструктивных схем.
В зданиях высотой более 12, 9, 5 и 3 этажей с наружными стенами, не участвующими в восприятии сейсмических нагрузок, при сейсмичности площадок строительства 7, 8, 9 и 10 баллов соответственно, как правило, следует предусматривать не менее двух внутренних продольных стен.
Примечание. Строительство зданий со стенами из монолитного железобетона предпочтительно осуществлять с применением инвентарной переставной опалубки (щитовой, блочной и объемно-переставной). Применение скользящей опалубки должно сопровождаться организационными и технологическими мероприятиями, исключающими возможность образования в монолитных стенах разрывов и пустот.
Для зданий с несущими стенами из монолитного железобетона могут применяться монолитные, сборно-монолитные или сборные перекрытия.
Монолитные и сборно-монолитные перекрытия рекомендуется проектировать в виде неразрезной железобетонной плиты.
Сборные перекрытия допускается выполнять из плоских или многопустотных железобетонных плит перекрытий, объединенных для совместной работы с помощью конструктивных мероприятий, указанных в п. 7.23в,г СНиП РК 2.03-30-2006.
При проектировании многоэтажных зданий с несущими стенами из монолитного железобетона допускается использовать зонирование несущих стен по высоте за счет назначения переменной толщины стен и применения различных классов бетона.
Толщину несущих монолитных стен следует назначать по результатам расчета, но не менее 120 мм для зданий высотой до 5 этажей и не менее 160 мм -для зданий высотой более 5 этажей (при толщине стен верхних пяти этажей не менее 120 мм).
Несущие монолитные стены могут выполняться из тяжелого, легкого и ячеистого бетона. Прочность бетона должна быть не ниже указанной в табл. 7.3 СНиП РК 2.03-30-2006.
Требуемую прочность бетона следует принимать по результатам расчетов, но не менее указанной в табл. 7.3 СНиП РК 2.03-30-2006.
Армирование монолитных железобетонных стен следует назначать по результатам расчета и по конструктивным требованиям.
Армирование монолитных железобетонных стен должно включать:
Вертикальную арматуру у торцовых граней стен, у граней проемов и в местах пересечения стен (периферийную арматуру);
Горизонтальную, вертикальную или наклонную арматуру поля стен (полевое армирование);
Горизонтальную или наклонную арматуру в вертикальных сопряжениях стен;
Горизонтальную, вертикальную или наклонную арматуру в сопряжениях стен с перекрытиями;
Горизонтальную, вертикальную или наклонную арматуру в перемычках.
Армирование периферийных участков стен следует осуществлять пространственными вертикальными каркасами, располагаемыми на участках протяженностью 0,1-0,2 от длины стены.
Продольную арматуру вертикальных каркасов периферийных участков следует принимать из стержней диаметром не менее 8 мм.
Хомуты арматурных каркасов периферийных зон следует выполнять вязаными и замкнутыми. Диаметр хомутов пространственных каркасов должен быть не менее 6 мм.
Полевое армирование стен, как правило, следует выполнять арматурными блоками из плоских вертикальных каркасов, объединенных горизонтальными стержнями.
Вертикальные каркасы следует устанавливать с шагом не более 400 мм. Продольную арматуру вертикальных каркасов следует принимать из стержней диаметром не менее 6 мм. Поперечные стержни следует принимать из стержней диаметром не менее 4 мм с шагом не более 500 мм.
Горизонтальные стержни следует принимать диаметром не менее 5 мм и устанавливать с шагом не более 400 мм. Горизонтальные стержни должны быть заанкеренными в зонах периферийного армирования.
Стыки продольной арматуры вертикальных каркасов периферийного и полевого армирования следует выполнять на высоте не менее 500 мм от плиты перекрытия.
В местах пересечения стен следует устанавливать горизонтальную арматуру, площадь сечения которой принимается по расчету, но не менее:
· для зданий высотой до 5 этажей включительно, возводимых на площадках сейсмичностью 7 баллов, - 1 см 2 на 1 м длины стыка;
· в остальных случаях - не менее 2 см 2 на 1 м длины стыка.
Наибольший диаметр стержневой арматуры, устанавливаемой в стенах зданий с несущими стенами из монолитного бетона, не должен превышать:
для тяжелого и легкого бетонов классов:
· В12.5 и ниже-0, 15 толщины стены и 25 мм;
· В15 и выше - 0, 20 толщины стены и 32 мм;
· для ячеистого бетона - 16 мм.
При конструировании железобетонных стен, помимо требований данного раздела, следует учитывать положения раздела 8 настоящих норм.
Лекция 26
Тема лекции 26.Принципы обеспечения сейсмостойкости монолитных железобетонных каркасных зданий
План лекции
· Железобетонные монолитные конструкции каркасных зданий.
· Особенности конструирования несущих элементов каркасных зданий.
Тезисы лекции
1. Каркасные здания. Конструктивные схемы каркасных зданий: рамные со всеми жесткими узлами сопряжений ригелей (поперечных и продольных) с колоннами; рамно-связевые; связевые; каркасно-стеновые.
2. Требование к выбору типа междуэтажных перекрытий и покрытий в каркасных зданиях с диафрагмами жесткости и в каркасных зданиях с ядрами жесткости.
3. Требование норм по расчету каркасных зданий рамно-связевых и связевых конструктивных систем.
4. Требование норм по назначению минимального и максимального армирования колонн железобетонных многоэтажных каркасных зданий (рамных, рамно-связевых, связевых и других). Конструктивные требования норм по назначению диаметра и шага хомутов во внецентренно-сжатых и изгибаемых элементах. Конструктивные требования норм по назначению диаметра и шага хомутов, устанавливаемых в колоннах каркасных зданий, запроектированных по рамным, рамно-связевым и связевым схемам.
5. Требования норм по усилению жестких узлов железобетонных рам. Требование норм по армированию поперечной арматурой (хомутами) участков ригелей и колонн, примыкающих к жестким узлам рам (в т.ч. к фундаментам).
6. Наружные и внутренние ограждающие стены и перегородки, выполняемые в виде заполнения, и не участвующие в восприятии расчетных сейсмических нагрузок на здание. Каркасные здания с диафрагмами жесткости. Каркасные здания с ядрами жесткости.
Основное содержание лекции
Каркасные здания
При проектировании каркасов зданий рекомендуется применять следующие конструктивные системы:
· рамные со всеми жесткими узлами сопряжений ригелей (поперечных и продольных) с колоннами;
· рамно-связевые;
· связевые;
· каркасно-стеновые.
Каркасы одноэтажных зданий могут проектироваться по следующим конструктивным схемам:
· комбинированной, в которой в одном направлении здания принимается рамная схема, а в другом - связевая;
· в виде стоек, защемленных в фундаментах и шарнирно сопряженных со стропильными конструкциями;
· в виде пространственных рамных конструкций шарнирно сопряженных с фундаментами.
В каркасных зданиях диафрагмы жесткости должны быть непрерывными по высоте. Диафрагмы допускается устанавливать с убывающей по высоте здания жесткостью (за счет уменьшения толщины диафрагм или сокращения их количества в верхних этажах).
В каждом направлении здания должно устанавливаться не менее двух диафрагм жесткости. Диафрагмы должны, как правило, располагаться симметрично в плане здания. Диафрагмы продольного и поперечного направлений целесообразно объединять в пространственные элементы.
В каркасных зданиях с ядрами жесткости последние рекомендуется располагать симметрично относительно центральных осей здания.
Для площадок сейсмичностью 9 и 10 баллов количество ядер жесткости следует принимать не менее двух на каждый отсек здания.
Междуэтажные перекрытия и покрытия зданий с диафрагмами и ядрами жесткости рекомендуется выполнять из монолитного железобетона. Соединения перекрытий с диафрагмами и ядрами жесткости должны обеспечивать совместную работу всех элементов конструктивной системы.
Расчет каркасных зданий рамно-связевых и связевых конструктивных систем следует выполнять с учетом податливости перекрытий.
Стыки арматурных выпусков ригелей и колонн на ванной сварке должны быть отнесены от грани колонн на расстояние не менее 1,5h, где h - высота ригеля.
В сборных каркасах высотой три и более этажей, возводимых в районах сейсмичностью 9 и 10 баллов, не рекомендуется применять бесконсольные сопряжения ригелей с колоннами.
Ограждающие ненесущие стены и перегородки каркасных зданий без вертикальных устоев жесткости, как правило, следует выполнять из облегченных панелей или других легких конструктивных элементов, не препятствующих деформированию каркасов при сейсмических воздействиях и не участвующих в их работе.
Заполнение, не участвующее в работе каркаса, следует проектировать в соответствии с положениями СНиП РК 2.03-30-2006 подраздела «Ненесущие ограждающие стены и перегородки».
Заполнение, участвующее в работе каркаса, рассчитывается и конструируется как диафрагма жесткости. При этом каркас здания должен рассчитываться на сейсмические нагрузки, составляющие не менее 25% от общей расчетной сейсмической нагрузки на здание.
Изделия и материалы кирпичной (каменной) кладки заполнения, участвующего в работе каркаса, должны отвечать соответствующим требованиям СНиП РК 2.03-30-2006 подраздела «Здания с несущими и самонесущими стенами из кирпичной (каменной) кладки».
В районах сейсмичностью 7 баллов, при высоте зданий не более 2 этажей, допускается применение неполного каркаса с опираниемкрайних ригелей на стены из кирпичной или каменной кладки. Стены таких зданий должны быть запроектированы в соответствии с положениями
СНиП РК 2.03-30-2006 подраздела «Здания с несущими и самонесущими стенами из кирпичной (каменной)кладки».
Применение самонесущих стен из кирпичной (каменной) кладки допускается в зданиях с шагом колонн не более 6 м и высотой не более: - 12 м- при сейсмичности площадки строительства 7 баллов;
9м- при сейсмичности площадки строительства 8 и 9 баллов.
Самонесущие стены должны быть запроектированы в соответствии с положениями СНиП РК 2.03-30-2006 подраздела «Здания с несущими и самонесущими стенами из кирпичной(каменной)кладки».
Применение самонесущих стен из кирпичной (каменной) кладки в районах сейсмичностью 10 баллов не допускается.
При конструировании элементов каркасов, а также диафрагм и ядер жесткости, помимо вышеуказанных требований, следует учитывать нижеуказанные положения разделов 8 и 9 СНиП РК 2.03-30-2006.
Общая площадь поперечного сечения продольной арматуры в железобетонных колоннах многоэтажных каркасных зданий не должна превышать 6% от площади поперечного сечения колонн.
Во внецентренно-сжатых и изгибаемых элементах хомуты должны ставиться по расчету и на расстояниях не более 400 мм и не более 12d,
где d
- наименьший диаметр продольных сжатых стержней.
Во внецентренно-сжатых элементах с площадью сечения продольной арматуры более 3% хомуты следует устанавливать на расстоянии не более 8d и не более 250 мм.
Шаг хомутов, устанавливаемых в колоннах каркасных зданий, кроме запроектированных по связевым схемам, не должен превышать 1/2h,
а в колоннах каркасных зданий, запроектированных по связевым схемам, - 3/4h
, где h
- наименьший размер сечения колонны.
Диаметр хомутов следует принимать не менее 8 мм.
Жесткие узлы железобетонных рам должны быть усилены сварными сетками, спиралями или замкнутыми хомутами, установленными с шагом не более 100 мм.
Участки ригелей и колонн, примыкающие к жестким узлам рам (в т.ч. к фундаментам), на расстоянии, равном полуторной высоте их сечения, должны армироваться замкнутой поперечной арматурой (хомутами), установленной по расчету, но с шагом не более 100 мм. Первый хомут должен располагаться на расстоянии не более 50 мм от грани узла.
Соединения рабочей арматуры (на сварке или без сварки) должны, как правило, располагаться вразбежку, с соблюдением соответствующих положений СНиП по проектированию железобетонных и бетонных конструкций.
Стыковые соединения арматуры на ванной сварке в инвентарных (съемных) формах и на сварке на остающихся стальных скобах-накладках допускаются при условии контроля качества их выполнения разрушающими методами
В зоне перепуска арматуры ригелей, стыкуемой внахлестку без сварки, шаг хомутов должен быть не более h /4.
Концы гнутых хомутов должны быть загнуты вокруг продольной арматуры и заведены вглубь сечения на длину не менее 6d хомута и не менее 8 см.
Лекция 27.
Монолитный железобетон является популярным строительным материалом, который используется при строительстве дорогостоящих объектов. Нашел свое применение при возведении торговых центров, зданий с большим количеством этажей и для сооружения авторских домов. Железобетонные конструкции называют монолитными, если их заливка осуществляется непосредственно на строительной площадке. Популярность монолитного домостроения обусловлена невысокой ценой, прочностью построек и способностью выдерживать большие нагрузки. Возведение монолитных железобетонных конструкций может осуществляться в любое время года, что значительно сокращает время на строительство зданий и сооружений.
Монолитные железобетоны имеют следующие преимущества:
- стойкость к воздействию огня;
- возможность собственноручного монтажа;
- минимальные физические затраты при возведении железобетонной монолитной конструкции;
- отсутствует необходимость в дополнительной технике и подъемных механизмах;
- стойкие к образованию коррозии;
- не поддаются окислению;
- одинаковый технологический процесс для всех циклов;
- скорость монтажа;
- способность противостоять большим нагрузкам;
- сравнительно низкая стоимость на монолитное домостроение;
- сейсмоустойчивость сооружений;
- спустя много лет эксплуатации, железобетонный материал способен увеличивать свои прочностные качества;
- долговечность;
- отсутствует потребность в большом количестве техники и оборудования;
- небольшой вес элемента, при строительстве которого не требуется возведение тяжелого фундамента;
- возможность применения любой планировки дома;
- снижение затрат на отделочные работы за счет гладкой поверхности материала;
- надежность и прочность.
Недостатки
Выделяют следующие недостатки:
- необходимость в применении шумоизоляционного материала;
- существуют сложности разборки;
- вероятность появления трещин, отслоек и других подобных деформаций;
- сложность монтажа опалубки;
- необходимость нанимать квалифицированных рабочих;
- потребность в прогревании бетона при возведении конструкции в холодное время года;
- надобность в укладке теплоизолирующего материала;
- обеспечение дополнительного ухода в период застывания раствора.
Какой толщины должна быть стена?
Толщина стен зависит от разновидности зданий. Для зданий с одним этажом выбирают стену толщиной не больше двадцати сантиметров, для сооружений с большим количеством этажей потребуются стены с толщиной не меньше 55 сантиметров. Таким образом, можно сделать вывод, что толщина железобетонных стен для разных построек колеблется от двадцати до 55 сантиметров.
Устройство монолитных стен
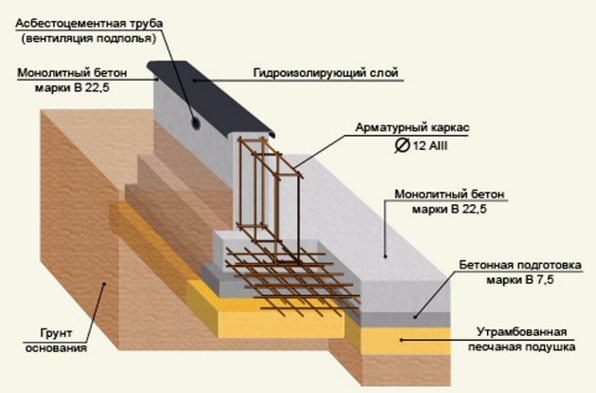
Монтаж монолитных конструкций различной толщины осуществляется непосредственно на строительной площадке. Первым делом, устанавливают опалубку, которая подходит под размеры постройки. Далее монтируют армирующий слой и приступают к бетонированию. Конструкция монолитов напоминает строительство , только в этом случае элементы изготавливают на заводе и доставляют на стройплощадку, где выполняют сборку.
Для монтажа сборной конструкции потребуется привлечение специальной техники и подъемных механизмов, а это дополнительные финансовые затраты и потребность в увеличенной рабочей силе. Однако при возведении монолита, не требуется транспортировка конструктивных элементов и применение спецтехники, что значительно сокращает расходы на строительство.
Опалубка
При возведении конструкций потребуется монтаж прочной опалубки, которая послужит защитой для вытекания раствора. Опалубка бывает таких видов:
- блочная, которая используется при монолитной заливке объектов без перекрытий;
- разборная, состоящая из отдельных частей обеспечивающие жесткость постройки;
- скользящая, которая применяется в строительстве многоэтажных зданий;
- пневматическая, имеет воздухопроницаемую прочную оболочку;
- несъемная, используется в роли декора;
- туннельная, необходима в постройках с перекрытием.
Процесс установки опалубки несложный и состоит из рытья котлована и монтажа щитов. Монтируя опалубку, важно следить за ровностью конструкции и избегать деформаций под воздействием больших масс бетонного раствора.
Для армирования вбирают двухслойный каркас, который предотвратит прогиб стен в результате нагрузки. При укладке продольной арматуры соблюдают шаг в двадцать сантиметров, при горизонтальной арматуре – в тридцать пять сантиметров. Армирующая сетка прокладывается по всему периметру опалубки.
Заливка
После установки армирующего слоя приступают к заливке бетонным раствором, который укладывают толщиной слоя не больше чем на пятьдесят сантиметров. Заливку смеси осуществляют только после высыхания предыдущих слоев. В процессе бетонирования раствор уплотняют вибратором, который удалит пузырьки воздуха. После заливки бетонную смесь оставляют сохнуть до достижения ее максимальных прочностных характеристик, на это уйдет месяц.
Спустя 30 дней приступают к утеплительным и финишным работам.
Где применяются?
Монолитный железобетон используется при строительстве жилых домов с несущими стенами, общественных и производственных сооружений, в зданиях с двумя этажами, а также при возведении каркасов с нетяжелыми ограждениями стен, перегородок из материалов высокого качества, которые способствуют уменьшению общей массы постройки. При строительстве промышленных конструкций, а именно в возведении стадионов, больших цехов, выставочных залов. Часто используются монолитные железобетоны при необходимости усилить фундамент, перекрытия, стены и колонны.
Заключение
Использование монолитных железобетонных конструкций имеют преимущественные аспекты относительно других строительных материалов. Его широкая область применения делает железобетонный монолит популярным элементом зданий и сооружений.
Однако выбирая материал, важно отталкиваться не только от его положительных качеств, но также и обращать внимание на недостатки, которые могут сыграть большую роль при возведении монолитных конструкций.
В наши дни используются разнообразные строительные материалы, как известные с древнейших времен, так и появившиеся недавно. Пустотные стены из железобетона стали возводить в ХХ веке. Вначале появился бетон, но в России и Англии одновременно его изобрели два человека, которые даже не знали друг друга. Это случилось в начале XIX века.
Создал железобетон вовсе не строитель, инженер, конструктор или архитектор. Простой французский садовник в 1867 году вместо деревянных цветочных кадок сделал бетонные, поместив проволоку в бетон.
Технология армирования стен
Проволока или стержни из стали, которые помещают в бетон для повышения его прочности на изгиб и растяжение, называют арматурой. Слово это на латыни обозначает «вооружение».
Вооруженный и укрепленный сталью бетон (точнее, уже железобетон) представляет собой совершенно новый материал, в котором компоненты обладают высокой прочностью сцепления. Правильно выполненная технология армирования стен сделает их крепкими на долгие годы. Для примера: стальной стержень диаметром 1,2 см, погруженный в бетон на 30 см, можно вытянуть из бетона, приложив силу около 400 кг. На это сцепление не влияют температурные перепады (и у стали, и у бетона коэффициенты теплового расширения почти не отличаются).
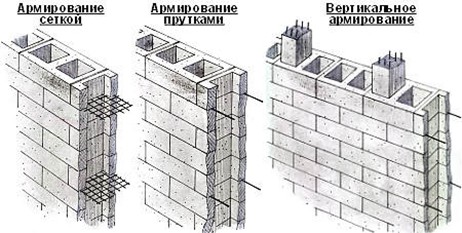
В железобетоне каждый компонент выполняет свою работу: нагрузку на растяжение несет сталь, на сжатие — бетон. И если сталь вооружает бетон, то бетон защищает сталь от коррозии и сильного нагревания, что позволяет железобетону выстоять при сильных пожарах. Поэтому армирование стен в строительстве применяют очень часто. Появляющиеся волосяные трещины неизбежны при предельных нагрузках, но эти трещины не критичны ни с точки зрения прочности материала, ни с точки зрения устойчивости стали к коррозии.
В строительной практике армируются такие железобетонные изделия: бетонные балки над дверными и оконными проемами, плиты перекрытия, панели из железобетона, балки мостов, ригели цеховых построек в промышленных зданиях, монолитные стены и др.
Для лучшей адгезии стальная арматура обладает рельефной поверхностью, на нее наносят различные насечки. Армирование монолитных стен будет намного качественнее и прочнее при соединении арматурного каркаса в одну сварную конструкцию.
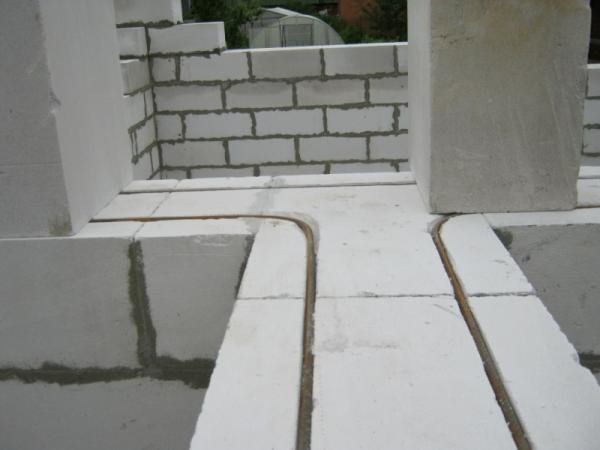
Не всегда материалы, из которых возводят те или иные сооружения, выносят предельные нагрузки. Поэтому армирование стен можно производить сеткой из стекловолокна. Покрытая слоем штукатурки, она тоже участвует в теплоизоляции сооружения. Таким образом, армирование монолитных стен — это один из важных шагов в строительстве домов.
Подпорные стены из монолитного железобетона
Монолитный железобетон представляет собой очень удачный и экономичный материал для создания следующих конструкций:
- полов;
- перекрытий;
- лестниц;
- кровель;
- стен, в том числе подпорных.
Подпорная стена возводится на тех склонах, где проектируются лестницы и площадки, поскольку ее прямое назначение — укрепление наклонных участков ландшафта и соединение различных участков с контрастным рельефом. Они удерживают грунт от сползания. Такие пустотные стены должны не только быть прочными инженерными конструкциями, но и вписываться в ландшафт, не уродуя его, а подчеркивая своеобразность и участвуя в формировании общей ландшафтной композиции.
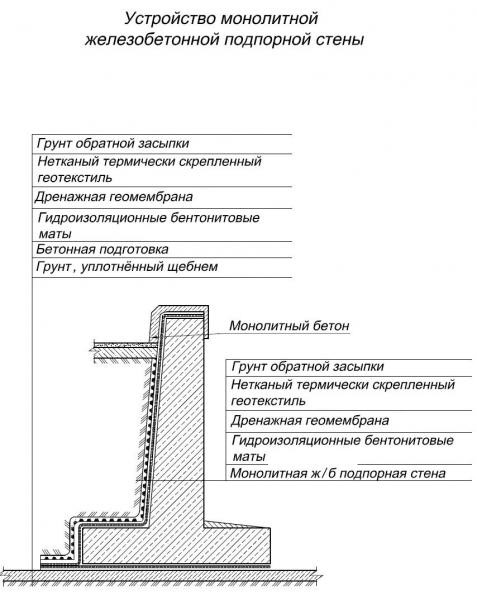
Подпорные стены выполняются из различных материалов, но железобетон является одним из самых удачных решений, поскольку при его использовании отпадает необходимость делать очень глубокую траншею под фундамент. Для подпорной стены из железобетона достаточно заглубления 15-20 см. Также благодаря высокой прочности железобетона подпорная конструкция полностью выполняет свою функцию при толщине 10 см. При этом за счет удешевления фундамента снижается стоимость и самой конструкции. При установке монолитных железобетонных подпорных стен в результате получается бесшовная конструкция, которая не только хорошо смотрится с эстетической точки зрения, но и более прочна и долговечна.
Сооружаются подпорные стены из монолитного железобетона методом отливки в опалубке, которая собирается в зависимости от конфигурации из досок или готовых щитов при криволинейной или ломаной конфигурации.
Первыми устанавливаются стенки опалубки на нижней террасе: готовые щиты монтируются к стенке выкопанной траншеи, соединяются между собой, а снаружи их снабжают подпорками, назначение которых — помочь щитам стоять прямо под весом бетонной массы.
Чтобы подпорная стена была ровной, опалубку изнутри обшивают соответствующим материалом, рубероидом или фанерой.
Когда первый ряд щитов уже установлен, можно ставить второй. Когда он готов, его укрепляют подпорками, как и первый, а вверху оба ряда соединяют между собой брусками.
Поскольку речь идет о железобетоне, внутри опалубки между щитами ставят 2 ряда стальной арматуры в виде сетки, но разрешено использование и металлических прутьев и даже обрезков водопроводных труб, соединенных проволокой.
При установке монолитной балки нельзя забывать о дренаже. Чтобы отводить грунтовую воду из-за монолитной стены из железобетона, в самой нижней части, на 5 см выше уровня поверхности, закладываются дренажные трубы из пластмассы нужного диаметра, расстояние между ними должно составлять 1 м.
Опалубка монолитных стен
Опалубка — это то, без чего невозможно формирование монолитных конструкций, как бетонных, так и железобетонных. Эти сооружения в зависимости от разборности делятся на 2 типа:
- съемная опалубка стен;
- несъемная опалубка.
Самые распространенные опалубки — съемные, в разнообразных вариациях. Название «съемная» предполагает, что щиты или доски, из которых сделана опалубка стен, убираются после полного высыхания бетона или первичного его схватывания. Съемная опалубка используется не только для формирования фундамента — она является полноценным участников возведения монолитных стен и каркасов многоэтажных зданий, с ее помощью изготавливаются пролеты лестниц и элементы декора.
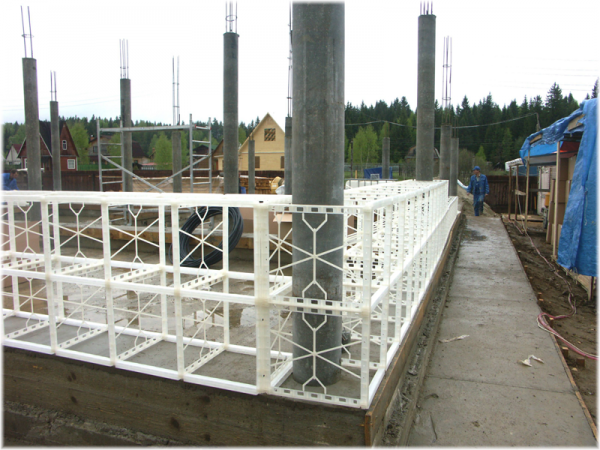
Что используется для изготовления съемной опалубки:
- древесина (щиты, доски и т.д.);
- фанера;
- стальной лист;
- алюминий (как лист, так и форма);
- поливинилхлорид;
- различные сочетания вышеуказанных материалов.
Независимо от материала опалубки существует ряд требований, одинаковых для всех:
- Каркас должен обладать достаточной жесткостью и быть зафиксированным на своем месте.
- Зазоры между элементами конструкции должны быть минимальными, для чего нужно тщательно их подгонять. Через зазоры может вытекать цементное молоко, из-за чего пострадает качество готового бетонного изделия.
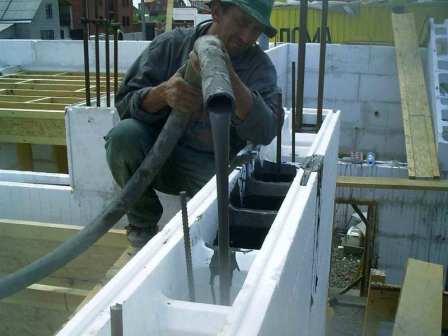
Несъемная опалубка стен — это конструкция, которая после заливки бетона и его застывания остается в бетонной массе как часть общей конструкции. Материалы, использующиеся для ее изготовления, должны быть:
- теплоизоляционными;
- прочными (при заливке бетона образуется значительное давление на конструкцию опалубки);
- с низкой теплопроводностью (монолитная конструкция из бетона обладает высокой теплопроводностью, поэтому бетон и опалубка должны составлять единую теплоизоляционную пару).
При использовании несъемной опалубки бетон более надежно, чем в съемной конструкции, защищен от различных неблагоприятных внешних факторов, в первую очередь от влаги и экстремальной температуры. Это своеобразный многослойный сэндвич из опалубки и бетона, где бетон обеспечивает прочность, а опалубка — термоизоляцию. В данном случае должна быть сделана расчетная схема с указанием пропорций смеси.
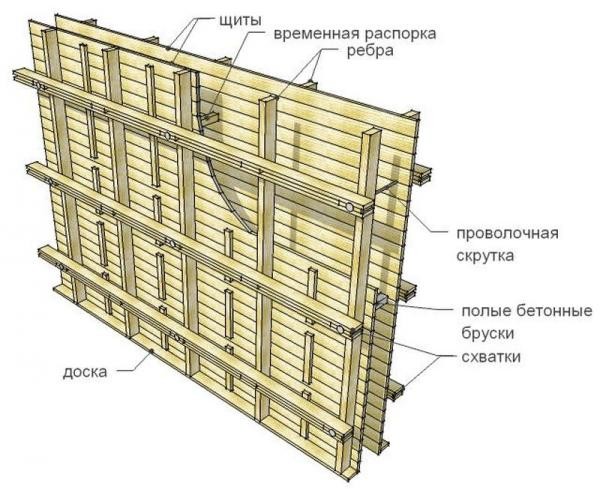
Несъемная опалубка стен может сооружаться и из облицовочных панелей, что очень выгодно для достижения эстетического результата. В частном домостроительстве очень интересны для использования в качестве опалубки такие теплоизоляционные материалы, как пенополистирол и арболит (материал из смеси отходов древесной промышленности с раствором цемента с последующим формированием полых блоков).
Возведение пустотных стен из железобетона
В силу специфичности конструкции пустотные стены нужно делать большей толщины, чем монолитные. Для возведения малоэтажного дома нужно брать пустотные железобетонные стены толщиной от 20 см. Полость, называемая еще воздушным карманом, располагается посередине стены, занимая от 3 до 6 см. Полость эту не оставляют пустой: карман заполняется пенопластом или минеральной ватой.
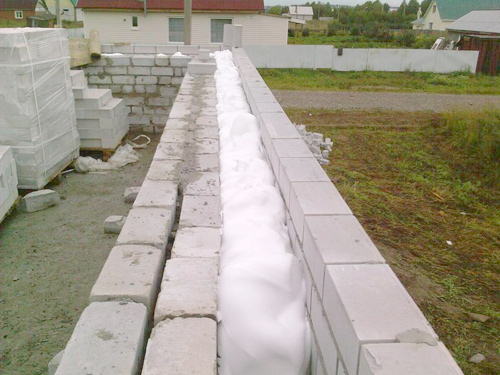
Использование пенопласта предполагает отсутствие дополнительной гидроизоляции. Этот материал просто помещают в опалубку с уже установленной арматурой и заливают бетонным раствором. Когда бетон застывает, стена получается с большой прочностью и хорошо удерживает тепло. Из минусов можно отметить то, что такое явление, как мостик холода, в данной конструкции неизбежно, но плюсом является то, что при утеплении можно обойтись меньшими средствами.
Когда для формования пустотных железобетонных стен используют в качестве утеплителя минеральную вату, вначале делают опалубку с полостью посередине, в опалубке выставляется арматура, затем заливается бетон. Через сутки опалубка снимается, а конструкция несколько дней отдыхает. Перед тем как заполнить воздушный карман минеральной ватой, утеплитель помещают во влагостойкие брикеты и уже в таком «зачехленном» виде монтируют в конструкцию. Особенность этих пустотных стен в том, что их нужно дополнительно упрочнять специальными колоннами.